大型CNC加工分中不准原因:
1、大型CNC加工操作员手动操作时不准确,手动操数有误。
2、大型CNC加工周边有毛刺。
3、分中棒有磁。
4、模具四边不垂直。
鸿灿笔者分享:大型CNC加工分中不准解决方法:
1、手动操作要反复进行仔细检查,分中尽量在同一点同一高度。
2、模具周边用油石或锉刀去毛刺在用碎布擦干净,*后用手确认。
3、对模具分中前将分中棒先退磁,(可用陶瓷分中棒或其它)。
4、校表检查模具四边是否垂直,(垂直度误差大需与钳工检讨方案)。分中不复杂,按照以上方法多操作几次即可,希望对大家有帮助。大型CNC加工也会发生对工件过切的现象。过切会直接影响工件加工精度,甚至导致工件报废。
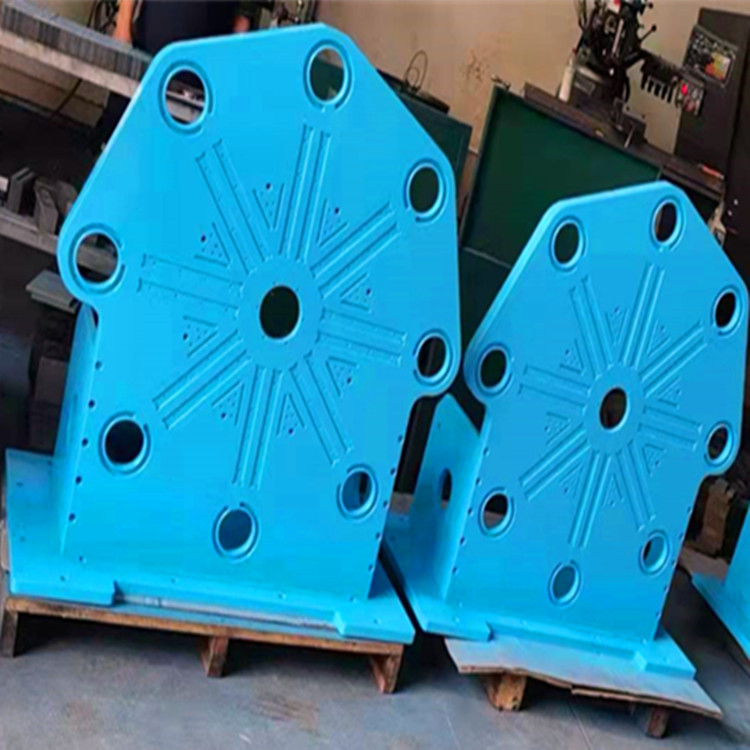
加工过程注意事项
1)在工件**面余量过大,用大刀手工锣去余量时,切记不要锣深。
2)加工较重要为**刀,因如果小心操作和核对便可得知刀长补、刀径补、程式、转速等等是否错误,避免损坏工件、刀具及机床。
3)按照以下的方式试切程序:
a)**点高度为较高升高100mm,用眼去感觉是否正确;
b)控制“快移”调至25%及进给调至0%;
c)当刀具接近(约10mm)加工面时,将机暂停;
d)检查剩余行程及程式是否正确;
e)再次开机后,一手放在暂停掣上,准备随时停机,另一手控制进给速度;
f)当刀具十分接近工件面时可再停止,必须一定要核对Z轴的剩余行程。
g)待加工切削行顺及稳定后,再将各控制调回正常状态。
4)输入程式名称后,用笔抄回屏上的程式名称,再与程序单进行核对,打开程式时,注意检查程序中的刀径大小是否与程序单相符,并在程序单上加工员签署栏中即时填写出档案名称与刀径大小,禁止事后或事前填写。
5)原则上在工件开粗时NC技工不得离开,如遇换刀或协助调较其他机床等,必须离开之情况时,须请其它NC组员或定时回来察看。
6)做中光时,NC技工应特别注意开粗时没有开到之处,防止刀具撞向此区域。
7)程序剪切。如遇程序在加工中发生中断而从头行过又浪费太多时间,应通知组长及编程师修改程序,剪去已行过部分。
8)程序异常。若遇程序出现异状况,且无把握时,可以吊高来行以观察其过程,然后决定下一步动作。
9)加工过程中编程师提供的行速和转速,NC技工可依情况酌情调节。但应特别注意小件铜公开粗时行速不能开快,以避免因震荡而导致工件松动。
10)工件加工过程中,NC技工应与散件图进行核对,看是否有异常况,一旦发现两者不吻合,必须立即停机通知小组负责人,核对是否有错误存在。
11)当采用**过200mm长刀具加工时,必须注意余量及进刀深度转速、行速等问题,以避免荡刀,同时转角位的行速更应予以控制。
12)对于程序单上要求检测刀具直径的,操作员必须认真负责,同时将测试之直径予以记录,**出公差范围的,应立即反映给小组负责人或换刀。
13)机床在自动操作或有空时,操作员应到工作站了解余下加工编程情况,准备及研磨好适当的刀具给下一加工备用,以免停机发生。
14)工艺失误是做成浪费时间的主要原因:错误运用不合适之刀具、加工先后安排失误、浪费时间在*加工或非电脑加工的位置、使用不当的加工条件(转速太慢、走空刀、刀路太密、进给太慢等等 ),上述事件发生时可于编程等联系。
15)加工过程中,必须注意刀具的磨损情况,应适当的更换刀粒或刀具,更换刀粒后,注意加工的相接边界是否吻合。
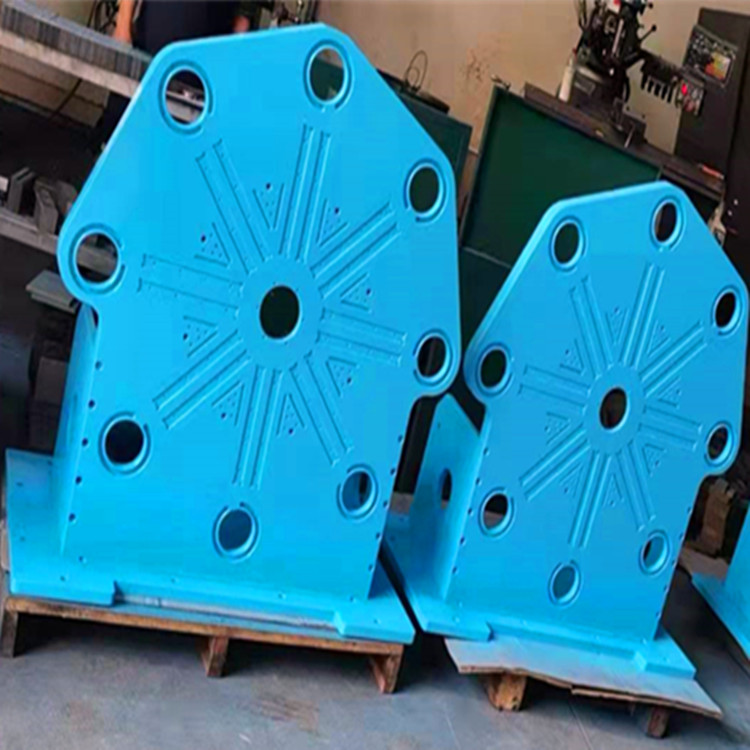
大型CNC加工之工件过切原因:
1、操作员操作不当。
2、切削余量不均匀。
3、切削参数不当。
4、弹刀,刀具强度不够太长或太小。
大型CNC加工之工件过切解决方法:
1、合理调整切削参数,余量大拐角处修圆。
2、利用机床SF功能,操作员微调速度使机床切削达到*佳效果。
3、大型CNC加工用刀原则:能大不小、能短不长。
4、添加清角程序,余量尽量留均匀,侧面与底面余量留一致。
大型CNC加工过程中出现的问题不能像普通机床那样可以方便的进行人为的调整,所以在大型CNC加工中必须注意加工过程的每一个细节,周密考虑,力求准确无误,避免过切问题的发生,做到不浪费,提高利用率。
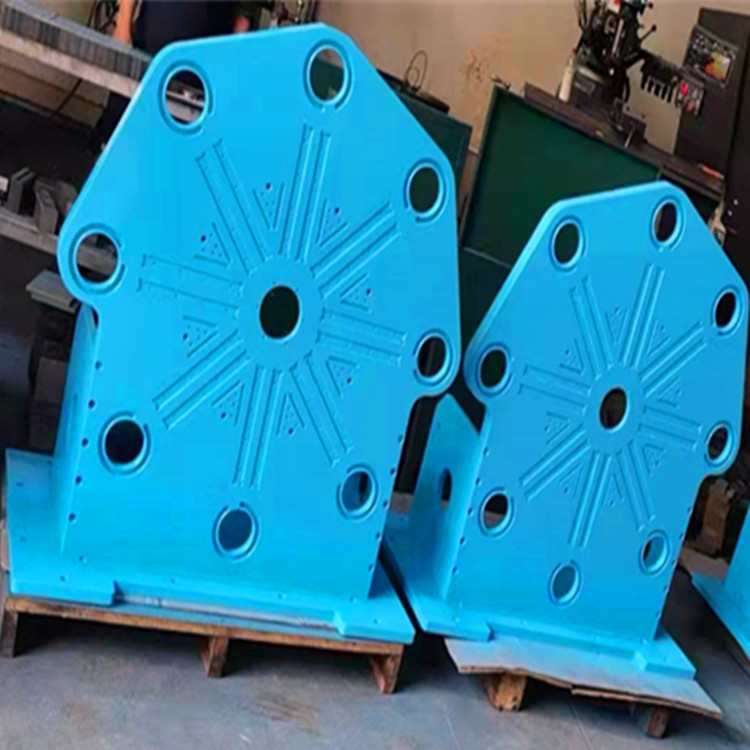
-/gjcggf/-
http://hongjia99.cn.b2b168.com