合理安排工序
高速切削时,由于加工余量大以及断续切削,因此铣削过程往往产生振动,影响加工精度和表面粗糙度。所以,数控高速切削加工工艺过程一般可分为:粗加工—半精加工—清角加工—精加工等工序。对于精度要求高的零件,有时需要进行二次半精加工,然后再进行精加工。粗加工之后,零件可以自然冷却,消除粗加工产生的内应力,减小变形。粗加工之后留下的余量应大于变形量,一般为1~2mm。精加工时,零件精加工表面要保持均匀的加工余量,一般以0.2~0.5mm为宜,使刀具在加工过程中处于平稳的状态,可以大大减少切削变形,获得良好的表面加工质量,保证产品的精度。

改善工件的夹装方法 对于刚性较差的薄壁铝件工件,可以采用以下的夹装方法,以减少变形:
①对于薄壁衬套类零件,如果用三爪自定心卡盘或弹簧夹头从径向夹紧,加工后一旦松开,工件必然发生变形。此时,应该利用刚性较好的轴向端面压紧的方法。以零件内孔定位,自制一个带螺纹的穿心轴,套入零件的内孔,其上用一个盖板压紧端面再用螺帽背紧。加工外圆时就可避免夹紧变形,从而得到满意的加工精度。
②对薄壁薄板工件进行加工时,选用真空吸盘,以获得分布均匀的夹紧力,再以较小的切削用量来加工,可以很好地防止工件变形。
另外,还可以使用填塞法。为增加薄壁工件的工艺刚性,可在工件内部填充介质,以减少装夹和切削过程中工件达变形。例如,向工件内灌入含3%~6%硝酸钾的尿素熔融物,加工以后,将工件浸入水或酒精中,就可以将该填充物溶解倒出。
合理安排工序 高速切削时,由于加工余量大以及断续切削,因此铣削过程往往产生振动,影响加工精度和表面粗糙度。所以,数控高速切削加工工艺过程一般可分为:粗加工-半精加工-清角加工-精加工等工序。对于精度要求高的零件,有时需要进行二次半精加工,然后再进行精加工。粗加工之后,零件可以自然冷却,消除粗加工产生的内应力,减小变形。粗加工之后留下的余量应大于变形量,一般为1~2mm。精加工时,零件精加工表面要保持均匀的加工余量,一般以0.2~0.5mm为宜,使刀具在加工过程中处于平稳的状态,可以大大减少切削变形,获得良好的表面加工质量,保证产品的精度。

数控机床加工产品材质繁多,其中铝件就是加工*多的之一。使用数控机床加工铝件时,想让加工尺寸更稳定,这些地方一定要注意。
1、机床的状态。加工稳定与否很大程度上取决于机床自身状态,加工前我们要对机床自身都检查完毕没问题后在启动设备。
2、材料冷却问题。工件在冷却后可能会出现变形的情况。这种情况往往难以避免,这时候就需要特别注意冷却液的使用。在进行在位测量时也要考虑材料变形的可能。
3、加工工艺。加工工艺不合理较易造成工件的尺寸误差。在保证基本加工工艺(如铣削数控加工的“先粗后精、先面后孔、先大面后小面”或者夹具使用中“减少装夹次数,尽量采用组合夹具”等基本加工工艺细节)的基础上,要尽量减少铁屑对铝件造成的加工误差。
4、参数设置。切削速度、进给量、切削深度与刀具补偿这些切削要素都会影响加工的稳定性,因此需格外注意。
5、刀具选择。加工铝件时尽量使用**刀具,这类刀具往往更有针对性。如铣铝**的铣刀通常前角和螺旋角会大一些,切削刃更锋利,更利于铝件的加工(如防积屑*),加工出来的表面质量也会更好。
6、应力方面。铝件材质较软,因此需要格外留意装夹力度。另外,在加工中,铝件开粗完好静置一段时间再进行下一道工序,以消除应力。
除此之外,铝件在加工中还要注意排屑以及切削液的使用量等问题。影响铝件加工稳定性的因素很多,因此在加工中要灵活应对,具体问题具体分析。稳定的机床,合理的加工工艺和刀具,以及操作员的技术水平都是影响产品质量的要素。
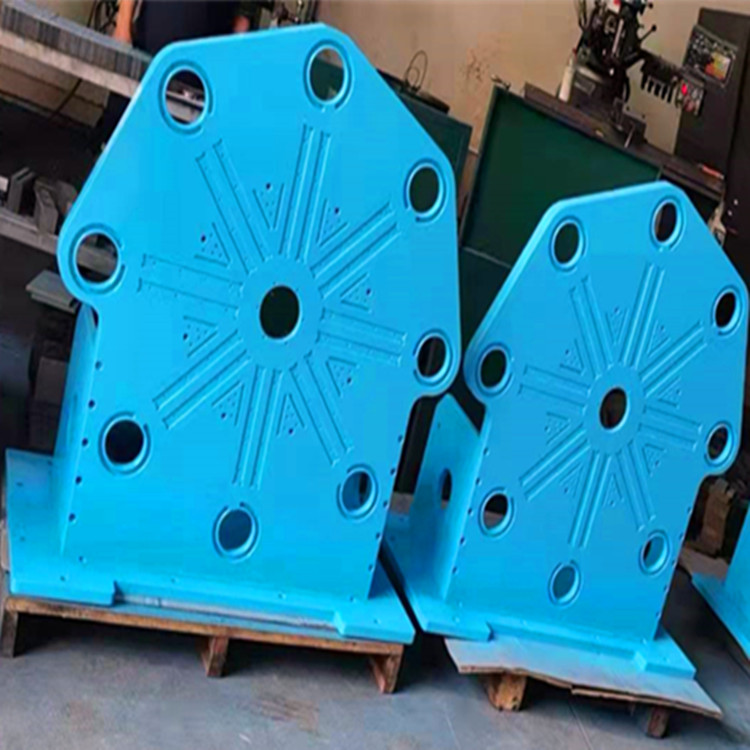
5、薄壁工件在加工时由于装夹产生变形,即使精加工也是难以避免的。为使工件变形减小到较低限度,可以在精加工即将达到最后尺寸之前,把压紧件松一下,使工件自由恢复到原状,然后再轻微压紧,以刚能夹住工件为准(完全凭手感),这样可以获得理想的加工效果。总之,夹紧力的作用点较好在支承面上,夹紧力应作用在工件刚性好的方向,在保证工件不松动的前提下,夹紧力越小越好。6、在加工带型腔零件时,加工型腔时尽量不要让铣刀像钻头似的直接向下扎入零件,导致铣刀容屑空间不够,排屑不顺畅,造成零件过热、膨胀以及崩刀、断刀等不利现象。要先用与铣刀同尺寸或大一号的钻头钻下刀孔,再用铣刀铣削。或者,可以用CAM软件生产螺旋下刀程序。影响铝件加工精度和表面质量的主要因素是该类零件加工过程中容易发生变形现象,这需要操作者具备一定的操作经验和技巧。
-/gjcggf/-
http://hongjia99.cn.b2b168.com