焊接:
焊接定义:被焊材料原子与分子距京达晶格距离形成一体
①分类:a 熔化焊:氩弧焊、CO2焊、气体焊、手工焊
b 压力焊:点焊、对焊、撞焊
c 钎焊:电铬焊、铜丝
② 焊接方式:a CO2气体保护焊
b 氩弧焊
c 点焊接等
d 机器人焊
焊接方式的选用是根据实际要求和材质而定,一般来说CO2气体保护焊用于铁板类焊搠;氩弧焊用于不锈钢、铝板类焊接上,机器人焊接,可节省工时,提高工作效率和焊接质量,减轻工作强度。
③焊接符号:Δ 角焊, Д、I型焊, V型焊接, 单边V型焊接(V) 带钝边V型焊接(V), 点焊(O), 塞焊或槽焊(∏), 卷边焊(χ), 带钝边单边V型焊(V), 带钝之U型焊, 带钝的J型焊,封底焊, 逢焊
④箭头线和接头
⑤焊接缺失及其预防措失
点焊:强度不够可打凸点,强加焊接面积
CO2焊:生产率高,能源消耗少,成本低,抗锈能力强
氩弧焊:溶深浅,溶接速度慢,效率低,生产成本高,具有夹钨缺陷,但具有焊接质量较好的优点,可焊接有色金属,如铝、铜、镁等。
⑥焊接变形原因:焊接前准备不足,需增加夹具
焊接治具不良改善工艺
焊接顺序不好
⑦焊接变形效正法:火焰效正法
振动法
锤击法
人工时效法
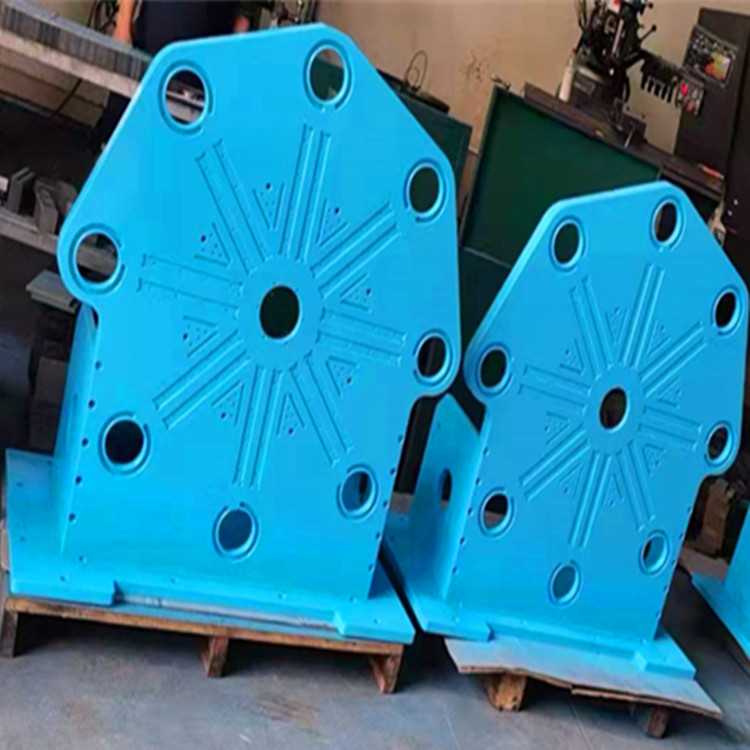
机械加工中哪些因素会造成工件变形
尤其在大型零件的结构上更应该做到结构合理。在加工前也要对毛坯硬度、疏松等缺陷进行严格控制,保证毛坯质量,减少其带来的工件变形。
02
工件装夹时造成的变形
工件装夹时,首先要选择正确的夹紧点,然后根据夹紧点的位置选择适当的夹紧力。因此尽可能使夹紧点和支撑点一致,使夹紧力作用在支撑上,夹紧点应尽可能靠近加工面,且选择受力不易引起夹紧变形的位置。
当工件上有几个方向的夹紧力作用时,要考虑夹紧力的先后顺序,对于使工件与支撑接触夹紧力应先作用,且不易太大,对于平衡切削力的主要夹紧力,应作用在后。
其次要增大工件与夹具的接触面积或采用轴向夹紧力。增加零件的刚性,是解决发生夹紧变形的有效办法,但由于薄壁类零件的形状和结构的特点,导致其具有较低的刚性。这样在装夹施力的作用下,就会产生变形。
增大工件与夹具的接触面积,可有效降低工件件装夹时的变形。如在铣削加工薄壁件时,大量使用弹性压板,目的就是增加接触零件的受力面积;在车削薄壁套的内径及外圆时,无论是采用简单的开口过渡环,还是使用弹性芯轴、整弧卡爪等,均采用的是增大工件装夹时的接触面积。这种方法有利于承载夹紧力,从而避免零件的变形。采用轴向夹紧力,在生产中也被广泛使用,设计制作**夹具可使夹紧力作用在端面上,可以解决由于工件壁薄,刚性较差,导致的工件弯曲变形。
03
工件加工时造成的变形
工件在切削过程中由于受到切削力的作用,产生向着受力方向的弹性形变,就是我们常说的让刀现象。应对此类变形在刀具上要采取相应的措施,精加工时要求刀具锋利,一方面可减少刀具与工件的摩擦所形成的阻力,另一方面可提高刀具切削工件时的散热能力,从而减少工件上残余的内应力。
例如在铣削薄壁类零件的大平面时,使用单刃铣削法,刀具参数选取了较大的主偏角和较大的前角,目的就是为了减少切削阻力。由于这种刀具切削轻快,减少了薄壁类零件的变形,在生产中得到广泛的应用。
在薄壁零件的车削中,合理的刀具角度对车削时切削力的大小,车削中产生的热变形、工件表面的微观质量都是至关重要的。刀具前角大小,决定着切削变形与刀具前角的锋利程度。前角大,切削变形和摩擦力减小,但前角太大,会使刀具的楔角减小,刀具强度减弱,刀具散热情况差,磨损加快。所以,一般车削钢件材料的薄壁零件时,用高速刀具,前角取6°~30°,用硬质合金刀具,前角取5°~20°。
刀具的后角大,摩擦力小,切削力也相应减小,但后角过大也会使刀具强度减弱。在车削薄壁零件时,用高速钢车刀,刀具后角取6°~12°,用硬质合金刀具,后角取4°~12°,精车时取较大的后角,粗车时取较小的后角。车薄壁零件的内外圆时,取大的主偏角。正确选择刀具是应对工件变形的必要条件。
加工中刀具和工件摩擦产生的热量也会使工件变形,因此在很多时候选择高速切削加工。在高速切削加工中,由于切屑在较短时间内被切除,绝大部分切削热被切屑带走,减少了工件的热变形;其次,在高速加工中,由于切削层材料软化部分的减少,也可减少零件加工的变形,有利于保证零件的尺寸、形状精度。另外,切削液主要用来减少切削过程中的摩擦和降低切削温度。合理使用切削液对提高刀具的耐用度和加工表面质量、加工精度具有重要作用。因此,在加工中为防止零件变形必须合理使用充分的切削液。
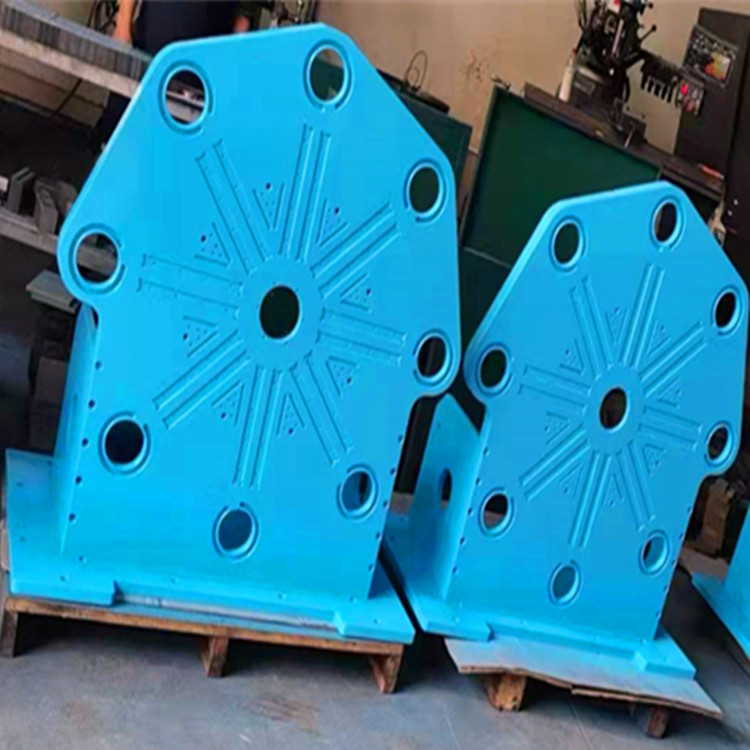
机械加工中哪些因素会造成工件变形
01
工件的材质和结构会影响工件的变形
变形量的大小与形状复杂程度、长宽比和壁厚大小成正比,与材质的刚性和稳定性成正比。所以在设计零件时尽可能的减小这些因素对工件变形的影响。
尤其在大型零件的结构上更应该做到结构合理。在加工前也要对毛坯硬度、疏松等缺陷进行严格控制,保证毛坯质量,减少其带来的工件变形。
02
工件装夹时造成的变形
工件装夹时,首先要选择正确的夹紧点,然后根据夹紧点的位置选择适当的夹紧力。因此尽可能使夹紧点和支撑点一致,使夹紧力作用在支撑上,夹紧点应尽可能靠近加工面,且选择受力不易引起夹紧变形的位置。
当工件上有几个方向的夹紧力作用时,要考虑夹紧力的先后顺序,对于使工件与支撑接触夹紧力应先作用,且不易太大,对于平衡切削力的主要夹紧力,应作用在后。
其次要增大工件与夹具的接触面积或采用轴向夹紧力。增加零件的刚性,是解决发生夹紧变形的有效办法,但由于薄壁类零件的形状和结构的特点,导致其具有较低的刚性。这样在装夹施力的作用下,就会产生变形。
增大工件与夹具的接触面积,可有效降低工件件装夹时的变形。如在铣削加工薄壁件时,大量使用弹性压板,目的就是增加接触零件的受力面积;在车削薄壁套的内径及外圆时,无论是采用简单的开口过渡环,还是使用弹性芯轴、整弧卡爪等,均采用的是增大工件装夹时的接触面积。这种方法有利于承载夹紧力,从而避免零件的变形。采用轴向夹紧力,在生产中也被广泛使用,设计制作**夹具可使夹紧力作用在端面上,可以解决由于工件壁薄,刚性较差,导致的工件弯曲变形。
03
工件加工时造成的变形
工件在切削过程中由于受到切削力的作用,产生向着受力方向的弹性形变,就是我们常说的让刀现象。应对此类变形在刀具上要采取相应的措施,精加工时要求刀具锋利,一方面可减少刀具与工件的摩擦所形成的阻力,另一方面可提高刀具切削工件时的散热能力,从而减少工件上残余的内应力。
例如在铣削薄壁类零件的大平面时,使用单刃铣削法,刀具参数选取了较大的主偏角和较大的前角,目的就是为了减少切削阻力。由于这种刀具切削轻快,减少了薄壁类零件的变形,在生产中得到广泛的应用。
在薄壁零件的车削中,合理的刀具角度对车削时切削力的大小,车削中产生的热变形、工件表面的微观质量都是至关重要的。刀具前角大小,决定着切削变形与刀具前角的锋利程度。前角大,切削变形和摩擦力减小,但前角太大,会使刀具的楔角减小,刀具强度减弱,刀具散热情况差,磨损加快。所以,一般车削钢件材料的薄壁零件时,用高速刀具,前角取6°~30°,用硬质合金刀具,前角取5°~20°。
刀具的后角大,摩擦力小,切削力也相应减小,但后角过大也会使刀具强度减弱。在车削薄壁零件时,用高速钢车刀,刀具后角取6°~12°,用硬质合金刀具,后角取4°~12°,精车时取较大的后角,粗车时取较小的后角。车薄壁零件的内外圆时,取大的主偏角。正确选择刀具是应对工件变形的必要条件。
加工中刀具和工件摩擦产生的热量也会使工件变形,因此在很多时候选择高速切削加工。在高速切削加工中,由于切屑在较短时间内被切除,绝大部分切削热被切屑带走,减少了工件的热变形;其次,在高速加工中,由于切削层材料软化部分的减少,也可减少零件加工的变形,有利于保证零件的尺寸、形状精度。另外,切削液主要用来减少切削过程中的摩擦和降低切削温度。合理使用切削液对提高刀具的耐用度和加工表面质量、加工精度具有重要作用。因此,在加工中为防止零件变形必须合理使用充分的切削液。
加工中采用合理的切削用量是保证零件精度的关键因素。在加工精度要求较高的薄壁类零件时,一般采取对称加工,使相对的两面产生的应力均衡,达到一个稳定状态,加工后工件平整。但当某一工序采取较大的吃刀量时,由于拉应力、压应力失去平衡,工件便会产生变形。
薄壁零件车削时变形是多方面的,装夹工件时的夹紧力,切削工件时切削力,工件阻碍刀具切削时产生的弹性变形和塑性变形,使切削区温度升高而产生热变形。所以,我们要在粗加工时,背吃刀量和进给量可以取大些;精加工时,刀量一般在0.2~0.5mm,进给量一般在0.1~0.2mm/r,甚至更小,切削速度6~120m/min,精车时用尽量高的切削速度,但不易过为高。合理选择好切削用量,从而到达减少零件变形的目的
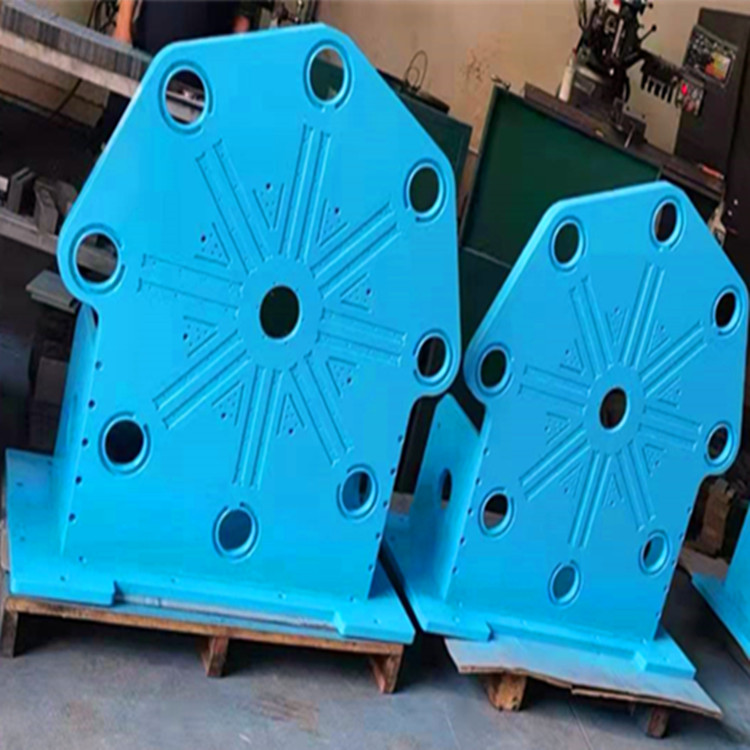
-/gjcggf/-
http://hongjia99.cn.b2b168.com